Description of Submersible Mixer Pump:
OHM series are Non-Clog Electric Submersible Pumps for Sludge, Sewage, Trash & Industrial Waste
The OHM wastewater submersible pumps are equipped with Vortex impellers, undoubtedly the best non-clog impellers ever invented for the handling of mud, raw sewage, viscous liquids, rags, wood chips and other solids. They pass solid up to 90% of pump outlet diameter. The solid die 25-70mm can go through from the pump channel.
-
Longer Power Cable – Standard 10.
-
Cast Iron Motor Housing – Superior abrasion resistance will not wear out like aluminum motor housings when pumping sandy water.
-
Three Seal Motor Protection - Motor is protected by double mechanical seals. Lower seal made of silicon carbide/silicon carbide and upper seal is made of carbon/ceramic. An additional lip seal has been installed above the impeller, to help prevent abrasives such as dirt, silt or sand, from entering into the seal chamber.
-
More Motor Protection – Winding protection and (IEC) Class F motor insulation allows the motor temperature to rise to 60°C, superior to pumps with Class A and B insulation. An automatic switch turns pump motor off if temperature and/or amp draw raises too high. When the motor cools the switch will automatically reset and the pump will turn back on.
-
Tough Pump Construction – Cast iron construction stands up to rough handling and pumping sandy water unlike pumps with soft resin impellers or plastic exterior components.
-
Option installation for support bracket and the movable-support bracket is for automatic coupling device, the water pump slide to the base along the rail and coupled to the water inlet automatically and seal reliably details as an auto-coupling diagram. Movable installation is supported by pump foot, which is not fixed on the base, it begins to work once wired with delivery hose, this model is usually applied to maintenance, temporary drainage during construction(only for pump of 4Kw below, details as movable Diagram
|
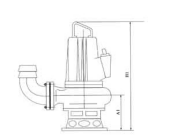
|
Support bracket for auto-coupling Diagram
|
Movable Diagram
|
In creating the cutter option to deal with wastewater ragging and fouling, an important concern was to keep efficiency as high as possible. Two designs worked well—the blade cutter and auger cutter. With a range of cutter solutions, users can choose the Croos cutter which will best suit their needs. Both provide Croos’s renowned quality and reliability. Here are the features, benefits, and differences of them both.
BLADE CUTTER Consists of a rotating and stationary cutter, utilizing a standard impeller.
• Minimal energy consumption (4% or less) for solution
• Designed to break up clogs/ragging
• Hardened cutter material
• Adjustable clearances
• Minimal flow restrictions
• Does not change external pump dimensions
• Retrofittable
CUTTER PUMPS TWO Cross PUMP SOLUTIONS In creating the cutter option to deal with wastewater ragging and fouling, an important concern was to keep efficiency as high as possible. Two designs worked well—the blade cutter and auger cutter. With a range of cutter solutions, users can choose the Croos cutter which will best suit their needs. Both provide Croos’s renowned quality and reliability. Here are the features, benefits, and differences of them both. WASTE WARRIOR AUGER CUTTER The more aggressive solution, featuring scythe-like edges from the impeller eye, sweeping all the area where the suction pipe meets the volute.
• Handles most aggressive and troublesome clogs and dragging
• Limited energy consumption (around 8%) for solution
• Hardened cutter material
• Insignificant flow restrictions
• Does not change external pump dimensions
• Retrofittable
No Flush Water or Packing: Through the back plate and sweeping vanes, flashless seal requires no flush water or packing, saving expense, service time, and messy drips. Extended Seal Life: Croos’s
flush less seal design has proven itself in the toughest applications, from manure slurry, starch recovery, and clear water, to food processing and self-priming applications – in some cases more than tripling the normally-expected seal life. Run-Dry Option: All pumps with Croos’s flashless seal system can be equipped with an optional Run-Dry feature, which serves to lubricate the seal faces even when there is no liquid in the pump casing. In situations where the pump must run dry for several hours, or where the pump may suddenly lose prime without being shut off, the RunDry feature is a must.
Better for Abrasive Applications: More resilient than packing and standard mechanical seals bathed in grit and other materials, flush less seal keeps solids away from the seal area for reduced seal wear. Greater Reliability: Through positive seating, end users can tell when the seal is perfectly fitted. With greater ability to withstand to grit, the flush less seal system results in longer intervals between service. Maintenance Savings: The end result of a longer-lasting seal is less downtime and lower maintenance costs over the life of the pump.